Body on Frame vs Unibody
Image Credit: C! Magazine / YouTube
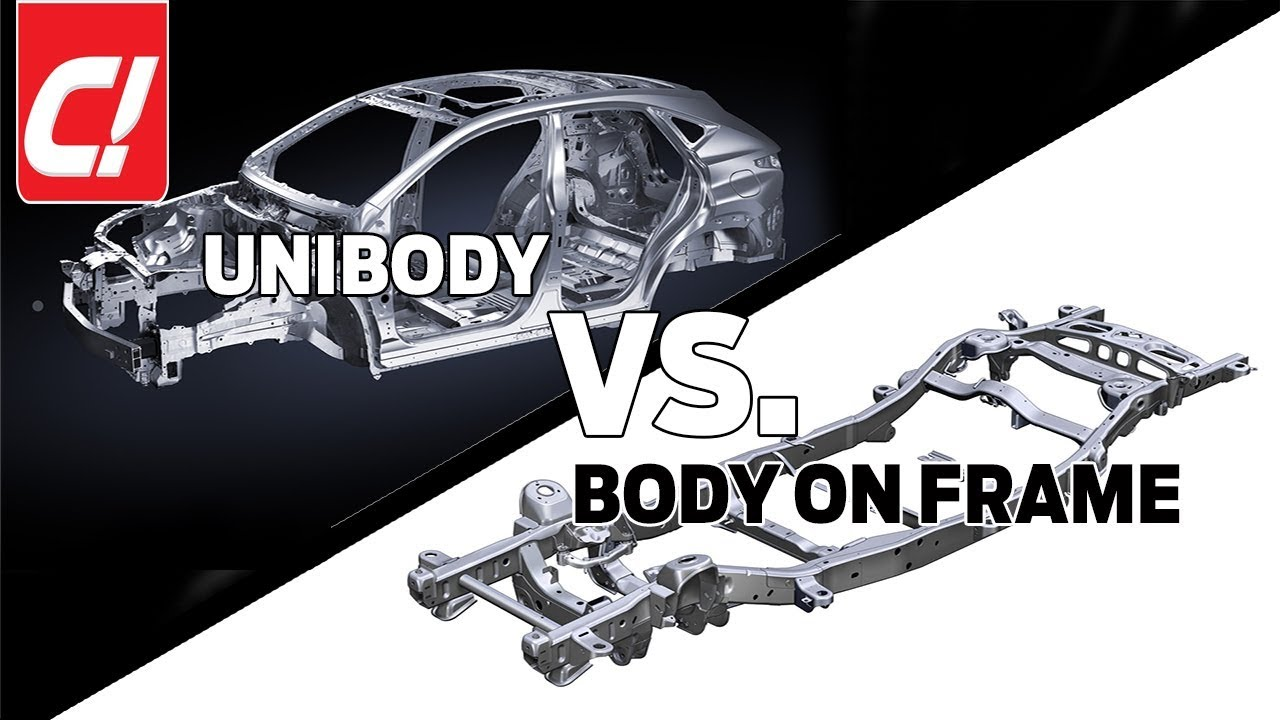
Cars come in many shapes and sizes and so do their respective construction methods: body-on-frame and unibody, as well as spaceframe and monocoque, two less common ways to build a car.
Here, we will explain what body-on-frame and unibody vehicles are, then cover the differences between them, and finally go through the upsides and downsides of these construction methods.
Image Credit: jrok, CC BY-SA 2.0 , via Wikimedia Commons
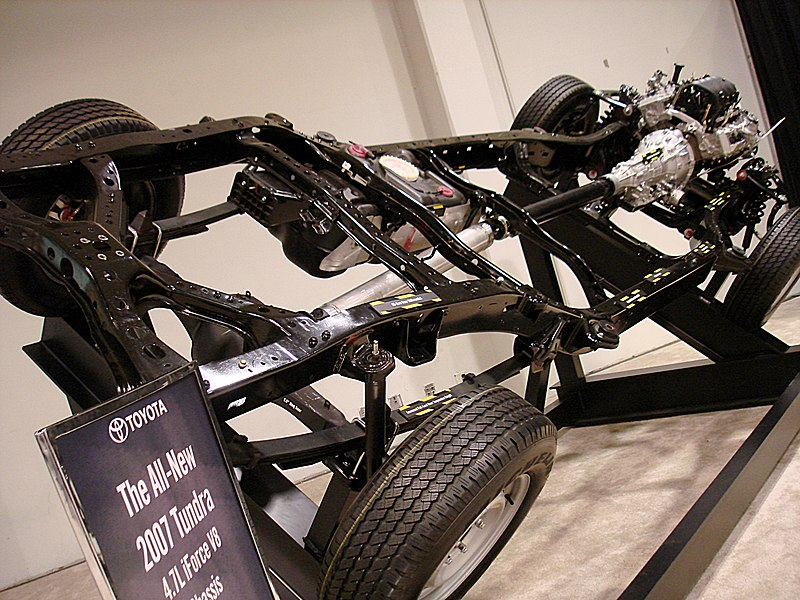
Body-on-frame
As its name suggests, body-on-frame construction has a car's bodywork attached to the chassis frame and it's the earliest construction method in the industry. Early automobiles used body-on-frame as a more convenient method enabling numerous bodywork variations on the same chassis.
Hailing back to horse carriages, the ladder frame is the earliest chassis construction, while other variations include a perimeter frame, backbone chassis, X-Frame, Y-Frame, and platform frame. All these variants were used for trucks, passenger cars, and some sports cars. One of the most famous and also the longest-running body-on-frame platforms was the Ford Panther, a full-size sedan and personal luxury perimeter frame used until the discontinuation of the 2012 Ford Crown Victoria.
Body-on-frame vehicles are still fairly common today and they are mostly full-size SUVs, pick-up trucks, and pick-up-derived SUVs. The reason is that body-on-frame vehicles are cheaper to produce, more rugged, and can handle larger payloads. All that combined makes body-on-frame an ideal method for producing dependable mechanical workhorses and capable off-roaders alike.
Still, body-on-frame comes with a certain number of drawbacks and design limitations. Given that a car's body is not a structural element, this construction lacks in the safety department as it's hard to engineer crumple zones and other structural safety features. Moreover, having only the underside as a structural element also translates to less direct handling on regular roads.
As far as ownership costs go, body-on-frame cars are broadly speaking easier and cheaper to repair. Since body panels are not structural elements, they are easier to replace and robust steel frames usually don't sustain damage in lighter accidents.
Thanks to growth in zero-emission transportation and due to the fact that these vehicles are still low volume compared to conventional petrol-burning counterparts, we're not yet done with body-on-frame cars, courtesy of so-called skateboard platforms.
Used in electric cars, these modular platforms house cars' powertrains upon which bodies are mounted. The first passenger car to employ a modern take on the platform underbody was the BMW i3, while other companies followed with their own renditions - Volkswagen MEB, Rivian Skateboard, Tesla Skateboard, and more.
1942 Unibody Nash Ambassador - Image Credit: public domain via picryl
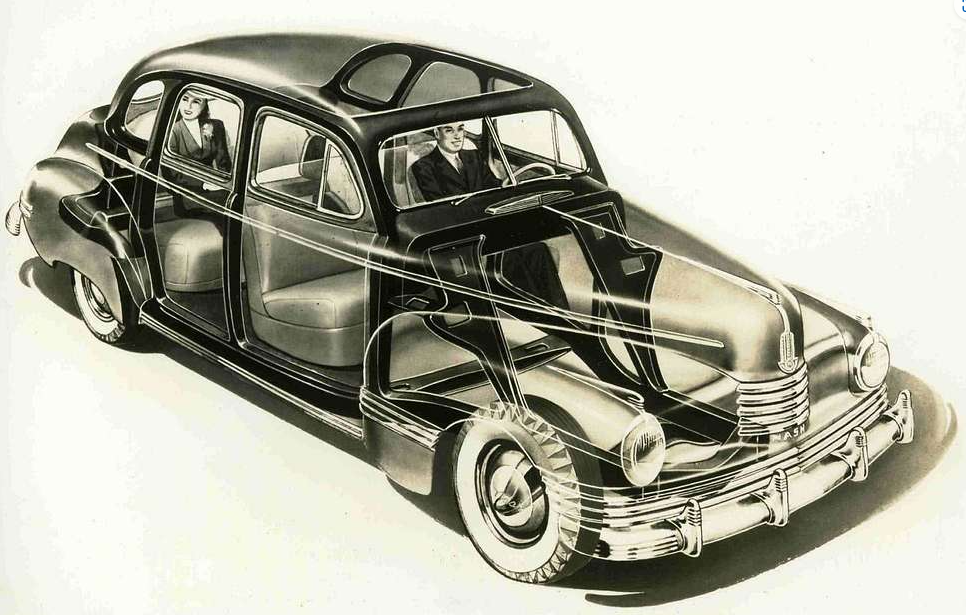
Unibody
As opposed to body-on-frame, unibody unites a car's upper body and the underbody into one integral structural element. Due to a number of benefits, unibody is now a universally accepted method for building passenger cars. Usually, unibody cars are constructed in steel, but some manufacturers opt for aluminum to achieve lower weight.
After Lancia experimented with unibody in 1922 with the Lambda, the first mass-produced unibody automobiles came out in the 1930s, with Citroën pioneering the construction method with the revolutionary Traction Avant. Gradually, more and more manufacturers followed suit until unibody construction eventually prevailed in passenger car markets.
Unibody design is also seen in subcompact and compact SUVs, and pick-up trucks as well. Yes, some compact trucks are built around a unibody structure and so is the iconic Ford F-150 which ditched the body-on-frame approach in favor of an aluminum unibody from the 2015 model year onwards.
Unibody design might be a more expensive manufacturing method as it doesn't allow as much freedom as body-on-frame construction, but it is still fairly reasonable. More importantly, unibody construction enabled the manufacturers to improve safety, thanks to integrating front and rear crumple zones, as well as rollover protections thanks to the cars' frames becoming structural elements. Unibody also provides better structural rigidity, leading to improved handling and overall ride quality.
On the other hand, unibody cars are usually written off in accidents as these frames are designed to absorb as much damage in order to keep the occupants safe. That being said, there's a much larger chance that a collision will compromise the car's structure, or at least lead to costly repair bills.
Mercedes-Benz W198 space frame chassis - Image Credit: Morio, CC BY-SA 3.0 , via Wikimedia Commons
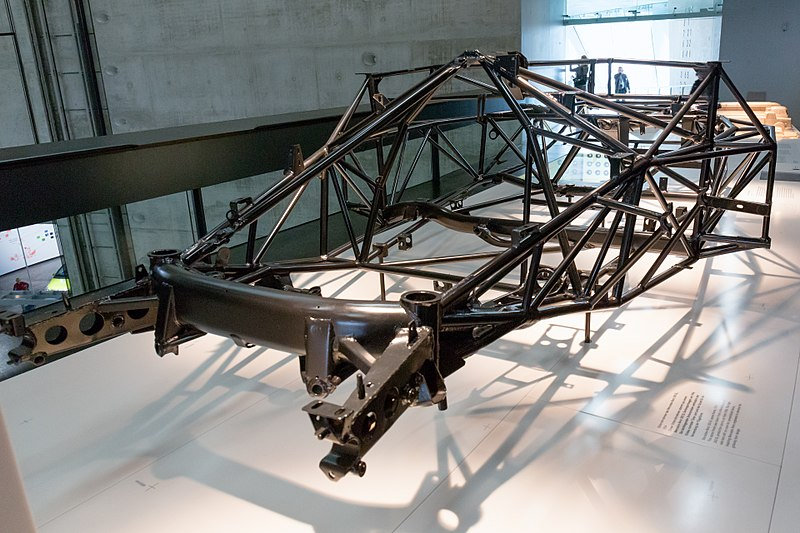
Space Frame Chassis
For decades, spaceframe construction was the go-to method for building sports cars as it provided necessary structural rigidity combined with low weight, all while being suited for low volume and handbuilt production.
Space frame chassis is an often intricate cage-like structure consisting of tubular steel of various grades and profiles. The space frame serves as a structural element, whereas body panels have very limited or no structural function.
The space frame chassis was largely abandoned by the end of the 20th century, but some sports cars still use some types of space frames. In addition to mainstream manufacturers, some niche sports cars like the Ariel Atom, some race cars, and various custom builds still rely on space frame construction, sometimes in steel and sometimes in aluminum.
GT500 monocoque - Image Credit: Tokumeigakarinoaoshima , CC0, via Wikimedia Commons
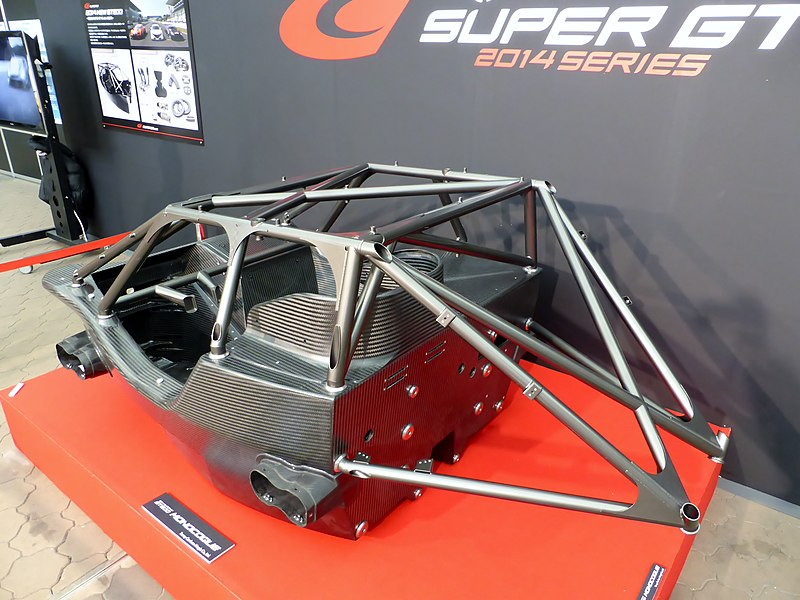
Monocoque
Monocoque chassis emerged from the airplane industry and it entered the automotive world through race cars. It later found use in low-volume, high-performance exotic automobiles and is here to stay.
Monocoque chassis is somewhat similar to a unibody, but it differs from it due to the fact that parts of a car's bodywork serve as its main structural element, making the passenger shell an exoskeleton. Monocoque constructions usually utilize steel subframes for carrying vital mechanics - engine and transmission, front and rear suspension.
In the beginning, the go-to material for these structural shells was aluminum, but today, you'll be more likely to see the word 'monocoque' next to 'carbon fiber. That's because carbon fiber provides exceptional rigidity paired with extremely low weight, making supercars exceptionally safe all while being as light as possible and in the automotive world, light always means fast.
Updated